Evolving OBC Designs for Higher Power Tiers and Voltages
不断改进 OBC 设计,适应更高的功率等级和电压
消费者需求不断攀升,电动汽车 (EV) 必须延长续航里程,方可与传统的内燃机 (ICE) 汽车相媲美。解决这个问题主要有两种方法:在不显著增加电池尺寸或重量的情况下提升电池容量,或提高主驱逆变器等关键高功率器件的运行能效。
为应对电子元件导通损耗和开关损耗造成的巨大功率损耗,汽车制造商正在通过提高电池电压来增加车辆的续航里程。
图 1:生产中的电动汽车以及所需的复杂系统
由此,800 V 电池架构越来越普及,并可能最终取代目前的 400 V 技术。然而,电池容量越大,所需的充电时间就越长,这正是车主的另一个顾虑,意味着若在抵达目的地前需中途充电,将要等待很长时间。
因此,就像需要提高电池电压一样,汽车整车厂商也必须跟上电动汽车车载充电器 (OBC) 的发展步伐,而首先要考虑的是必须支持 800 V 电池架构和处理更高的电压。为此,现行的标准 650 V 额定芯片元件需过渡到额定电压最高达 1200 V 的芯片元件。此外,为加快电池充电速率,对更高额定功率 OBC 的需求也在日益增长。
消费者迫切需要更出色的性能
OBC 能够将交流电转换为直流电,因而可以让汽车利用电网等交流电源进行充电。充电站的输出峰值会明显限制充电速度,同样的,OBC 的峰值功率处理能力也是充电速度的一大影响因素。
在目前的充电基础设施中,充电桩分为三个等级:
1 级的最大功率为 3.6 kW
2 级的功率为 3.6 kW 到大约 22 kW ,与 OBC 的最大容量相当
3 级提供直流电,无需使用 OBC,功率为 50 kW 到 350+ kW
尽管速度较快的 3 级直流充电站已投入使用,但其在全球范围内分布有限,因此 OBC 仍然不可或缺。此外,许多企业正尽可能提高现有 2 级充电基础设施的性能并促进更高电压电池技术的采用,市场对更高能效 OBC 的需求预计仍将持续增长。
表 1:OBC 的不同功率等级及其对 80 kWh 电池充电时间的影响
表 1 列举了常见的 OBC 功率等级及大致充电时间。为加快充电速度、满足消费者需求,行业已开始转向更强大的三相 OBC。然而,电动汽车的实际充电时间取决于多个因素。
首先我们需要明确一点,充电并不是一个线性过程。当电池接近满容量(通常超过 80%)时,充电速度会减慢,以保护电池健康。简单来说,电池电量越满,接受电能的速度就越慢。电动汽车通常不是满电状态,许多电动汽车制造商通常也不建议频繁待电量耗至 0% 再充满至 100%,而是只需充一部分(例如最高充到 80%),这样可显著缩短充电时间。此外,电气化趋势正逐渐延伸到公共汽车、货车、重型车辆和农业用车等各种车辆类型甚至是船舶,OBC 还将继续发展,目标是实现 22 kW 以上更高功率等级。
汽车整车厂商可以通过构建更强大的 OBC 来提高 2 级充电站的充电速度,但这需要利用经济高效且性能可靠的电子元件,来实现更高的电压(800 V,而非 400 V)和更高的功率等级。
更高性能 OBC 的关键设计考虑因素
对于更高性能的 OBC,除了额定功率和电池电压之外,还有许多因素需要考虑。其中包括散热管理、封装限制、器件成本、电磁兼容性 (EMC) 以及对双向充电的潜在需求。
谈到散热管理,很容易想到增加 OBC 的尺寸和重量。然而,这种简单的方案并不理想,因为电动汽车的空间有限,难以容纳过于庞大 OBC,而且重量增加也会导致缩短车辆的续航里程。
800 V 电池架构可以带来诸多益处,例如减少导通损耗、提高性能、加快充电和电力输送速度等,但也为设计师带来了许多复杂难题:
器件供应:寻找适合 800 V 安全运转的器件可能会很困难。
降额以确保可靠性:即使是合格的器件也可能需要降额,也就是以低于最大容量的功率运转,以确保长期可靠性。
安全问题:更高电压的系统需要强大的绝缘和安全功能。
测试和验证:验证高电压系统更为复杂,可能需要专门的设备和专业知识。
为此,需要用到击穿电压更高的元件,对于 MOSFET 而言尤其如此。事实证明,在需要更快 MOSFET 开关的更高电压应用(例如 OBC)中,改用高性能碳化硅 (SiC) 元件将大有裨益。开发 PCB 布局时,考虑电压等级也至关重要,因为可能需要相应地扩大元件间距和 PCB 走线之间的距离。同样,暴露于更高电压的其他器件(例如连接器、变压器、电容)也需要更高的额定值。
改进 OBC 设计,提升性能和功能
安森美 (onsemi) 是一家值得信赖的高功率汽车应用功率模块供应商,可以为向 800 V 电池系统过渡提供强大支持。安森美先进的 EliteSiC 1200 V MOSFET 和汽车功率模块 (APM) 能够实现更高的功率密度,在汽车设计领域一直深受认可。
图 2:EliteSiC 1200V MOSFET 采用 TO247-4L 封装,提供开尔文源极连接(第 3 根引线),可消除栅极驱动环路内共源极寄生电感的影响
APM32 功率模块系列集成安森美先进的 1200 V SiC 器件,针对 800 V 电池架构进行了优化,更适用于高电压和功率级 OBC。APM32 系列包括用于功率因数校正 (PFC) 级的三相桥模块,例如采用 1200 V 40 mΩ EliteSiC MOSFET(集成温度感测)的 NVXK2VR40WDT2。该模块专为 11 – 22 kW OBC 终端应用而设计。
相较于分立方案,APM32 模块技术具有多种优势,包括尺寸更小、散热设计更佳、杂散电感更低、内部键合电阻更低、电流能力更强、EMC 性能更好、可靠性更高等,从而有助于创建高性能双向 OBC(图 3)。这不仅能够增强车辆 OBC 的功能,还能让电动汽车充当移动的电池储能器。
图 3:采用 EliteSiC 1200V APM32 功率模块的高功率 (11 kW-22 kW) 双向 OBC 方案
图 3 的 OBC 功率级示例中包含升压型三相 PFC 和双向 CLLC 全桥转换器,用于提供必要的功率和电压处理及先进的双向充电功能。
在全球各地逐渐转向太阳能和风能等可持续能源之际,电网的电力供应有时可能供不应求。充满电的电动汽车能够作为重要的储能资源,用来支援电网的峰值需求,或者在建筑物主要电源受损的紧急情况下使用。利用安森美 APM32 等模块,OBC 可以实现电动汽车电池的双向能量传输。由此,电池存储的能量可以短暂地为房屋供电,之后还能随时充电。
可靠的设计和供应
与一些将封装技术外包的竞争对手不同,安森美的 APM 系列均在内部设计和制造,因而能够更好地掌控散热优化。此外,安森美为制造商提供了一系列封装和制造选项,包括裸片、分立元件或模块,从而确保有合适的方案支持任何先进的 OBC 设计。
结论
OBC 技术正蓬勃发展,不仅能帮助汽车制造商满足消费者对电动汽车的需求,还能有效应对 800 V 电池架构等新技术趋势。利用安森美系统方案(例如 APM32 功率模块),汽车设计人员可以简化流程并有效满足新需求,从而在大量减少设计工作的同时,确保更高的质量、可靠性和供应链一致性。
此外,安森美还提供广泛的技术支持、仿真及其他电源方案,其中包含 EliteSiC 1200 V M1 和 M3S MOSFET、EliteSiC 1200V D1 和 D3 二极管,以及电隔离栅极驱动器、CAN 收发器和可复位保险丝等配套器件,旨在助力实现全面、高性能的 OBC 设计。
上一篇:满电续航逼近千里,韩国公布固态电池使用成果
下一篇:留给油车的时间不多了?松下新电池技术再发豪语
推荐阅读最新更新时间:2024-11-11 12:01
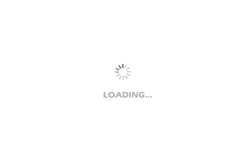
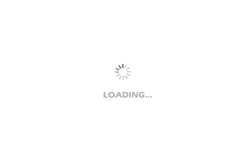
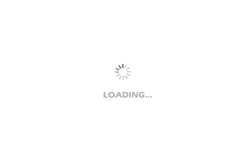
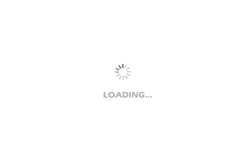
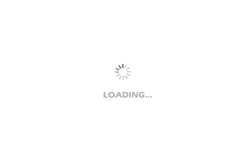

- 1389510A+简约时钟02
- 1588AUR矩阵时钟
- 1号工程(新工程)
- EVAL-ADN469xEFDEBZ,用于 ADN4692E 全双工 M-LVDS 收发器的高速评估板
- S32V2视觉和传感器融合低成本评估板
- AKD4388-SB,AK4388 192kHz 采样 24Bit Delta Sigma DAC 评估板
- AD9219-65EBZ,用于评估 AD9219 四通道、10 位、65 MSPS 串行 LVDS ADC 的评估板
- DC2392A,用于 LTC7860 高压开关浪涌抑制器的演示板
- MCP1525 的典型应用,2.5V 和 4.096V 电压基准基本配置
- NCV33074ADTBR2G 运算放大器用作晶体管驱动器的典型应用